In the dynamic landscape of manufacturing, the efficiency and lifespan of grinding wheels are pivotal factors that significantly impact productivity and costs. There is a growing interest in optimizing these aspects of grinding wheel performance as manufacturers strive to enhance their competitiveness.
Strategic Selection of Grinding Wheels
Material - Specific Choices
Selecting the appropriate grinding wheel material is the cornerstone of efficient grinding. For instance, when dealing with carbide materials, diamond grinding wheels are highly recommended. Their exceptional hardness and wear resistance enable precise and rapid material removal, boosting efficiency. In contrast, CBN (cubic boron nitride) grinding wheels are the go - to option for steel processing. CBN's high heat resistance effectively mitigates the risk of burns during grinding, ensuring both quality and extended wheel life.
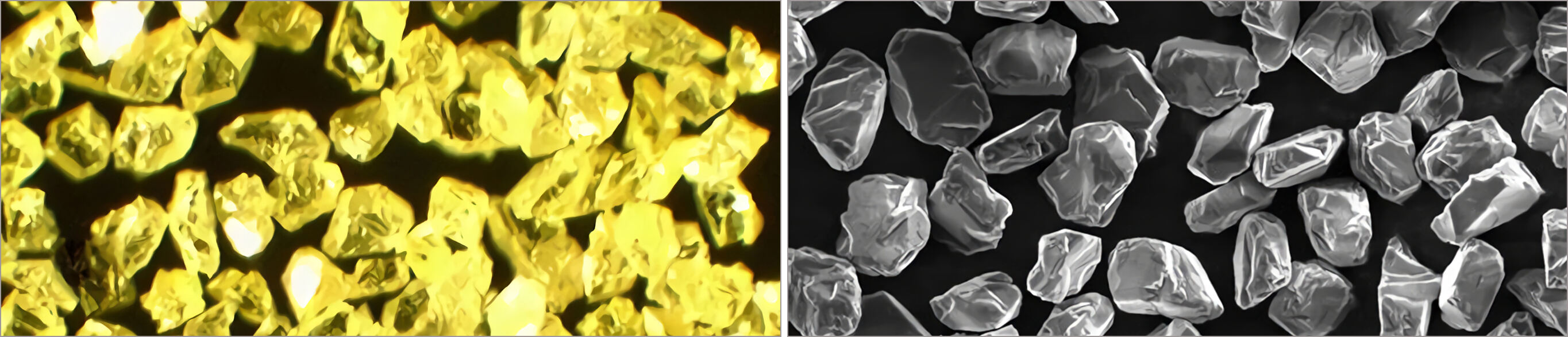
The choice of abrasive grain size also plays a crucial role. Coarse - grained wheels are ideal for rough grinding operations, where rapid material removal is the priority. They can quickly eliminate large amounts of material, but the resulting surface finish may be relatively rough. On the other hand, fine - grained wheels are reserved for precision grinding and finishing processes. Although the material removal rate is slower, they can achieve a smoother surface finish, which is essential for applications requiring high - precision components.
Grinding speed, feed rate, and depth are interrelated parameters that need to be carefully calibrated. Increasing the grinding speed can enhance the cutting efficiency, but it must be balanced with the risk of overheating. Excessive speed can lead to thermal damage to the workpiece and accelerated wear of the grinding wheel. Similarly, the feed rate should be adjusted according to the workpiece material and the desired surface quality. A higher feed rate can increase productivity, provided that the surface finish and wheel life are not compromised. The grinding depth, too, should be optimized. While a larger depth of cut can remove more material per pass, it may cause higher stress on the wheel and the workpiece, potentially leading to wheel breakage or workpiece deformation.
Coolant is not just a heat - reducing agent; it is a key factor in improving grinding efficiency and wheel lifespan. A high - quality coolant with excellent cooling, lubricating, and cleaning properties can significantly reduce the temperature at the grinding zone. This, in turn, minimizes thermal damage to the workpiece and slows down the wear of the grinding wheel. The coolant's flow rate and pressure are also important. Sufficient flow ensures effective heat dissipation, while proper pressure helps to flush away debris, preventing wheel clogging and maintaining a clean cutting surface.
Grinding wheel dressing is an essential practice for maintaining optimal performance. Over time, the abrasive grains on the wheel's surface become dull, and the wheel may develop an uneven shape. Dressing restores the wheel's sharpness and corrects its geometry. Diamond - based dressing tools, such as diamond rolls or single - point diamond dressers, are commonly used. The dressing frequency depends on the grinding application and the type of wheel. For high - precision grinding, more frequent dressing may be required to ensure consistent results.
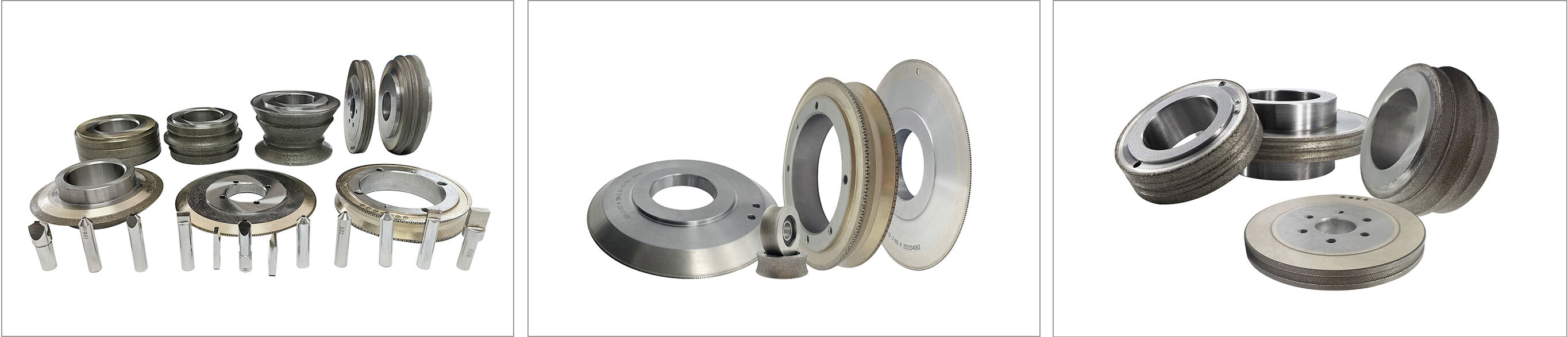
Proper storage and handling of grinding wheels are often overlooked but are critical for their longevity. Grinding wheels should be stored in a dry, cool environment away from direct sunlight and extreme temperatures. Moisture can cause corrosion in some types of wheels, especially those with metal components. Additionally, wheels should be handled with care to avoid impacts or drops, as even minor damage can compromise their structural integrity and performance.
Innovations in bonding systems are revolutionizing grinding wheel performance. Newer bond materials, such as advanced resins and ceramics, offer improved strength and heat resistance. For example, vitrified bond grinding wheels are known for their high stiffness and excellent shape retention, which is beneficial for precision grinding applications. These bonds can withstand higher temperatures and forces, enabling more efficient grinding and longer wheel life.
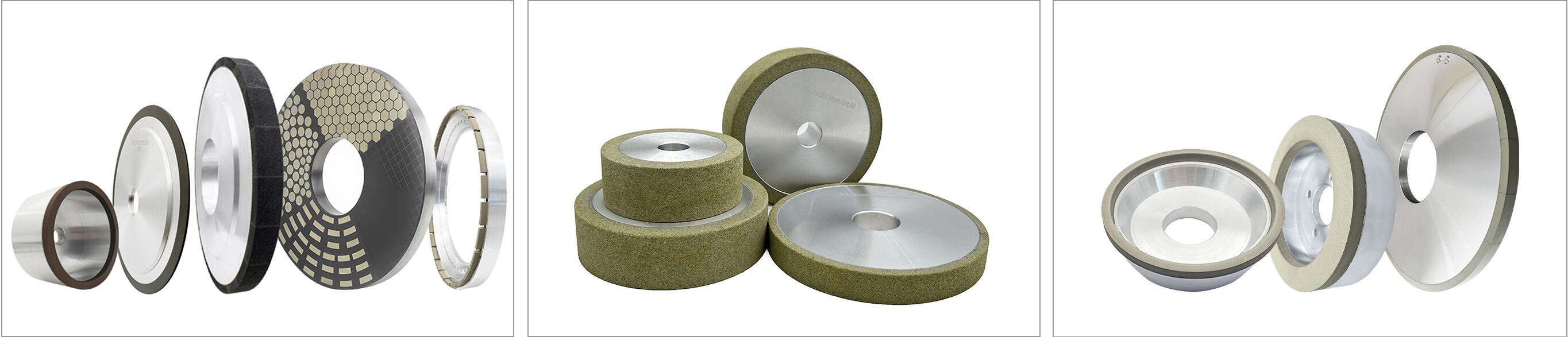
Hybrid grinding wheels, which combine different abrasive materials or bond types, are becoming increasingly popular. These wheels can leverage the advantages of multiple materials, such as the hardness of diamond and the heat resistance of CBN. Multilayered wheel designs, on the other hand, allow for different functions at different layers. For instance, a coarse - grained outer layer can be used for rapid material removal, while a fine - grained inner layer can be reserved for finishing, resulting in a more versatile and efficient grinding solution.
By implementing these strategies, manufacturers can significantly enhance the efficiency and lifespan of their grinding wheels, leading to improved productivity, reduced costs, and higher - quality output in the manufacturing process.
We sincerely invite manufacturers to engage in in-depth discussions with us regarding the grinding wheel industry. Leveraging our expertise in precision grinding technology, production process optimization] and a proven track record of collaborating with industry leaders, we are committed to addressing core challenges such as operational efficiency enhancement, cost optimization, and quality control refinement.